Waste Minimisation
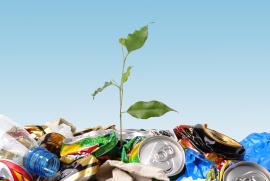
Every unit of material sent to waste carries a disposal cost. However the true cost of waste is more than just the cost of disposal. It also includes the additional cost of raw materials, energy and labour involved in making the product in the first place. This can be 5–20 times higher than the cost of disposal. So waste reduction programmes offer businesses a double saving.
Excessive waste at the end of a product's life is often due to the inefficient use of resources when it was produced. Dealing with waste has an impact on the environment so it makes sense to address the initial design of products to sustain our natural resources and the environment.
Why manage waste?
As well as making good financial sense, effective waste management helps organisations to become compliant with increasingly strict international legislation designed to limit the environmental impact of landfill sites.
In New Zealand, the Waste Minimisation Act (2008):
- Applies a levy on all waste disposed of in landfills to generate funding to help local government, communities and businesses reduce the amount of waste
- Encourages and, when necessary, makes producers, brand owners, importers, retailers, consumers and other parties take responsibility for the environmental effects of their products through product stewardship schemes
- Enables regulations which can make it mandatory for certain groups (for example, landfill operators) to report on waste to improve information on waste minimisation, and
- Establishes a Board to give independent advice to the Minister for the Environment on waste minimisation issues
Managing waste makes good financial sense
Most companies assume that a significant investment is required to reduce waste and implement a recycling scheme at their workplace. The reality is that most waste reduction projects give payback in months rather than years. For companies who are at or near the disposal stage of the hierarchy there is a good chance that there are low and no cost actions you can take that will have immediate payback.
For example, a Waikato plastics company was generating 6.55 tonnes of plastic waste in sprues and rejects. This waste was being sent to a recycler and earning 25c per kg but the virgin raw material costs $2-$6 per kg. The company is now regrinding onsite rather than sending waste to the recycler, saving them $16,000 a year in raw material costs. Minus the cost of running the grinder which is just $600 a year this results in annual cost savings of $15,400/year. With upfront costs for a grinder of $10,000 this initiative paid for itself within 8 months.
How much waste do we generate?
New Zealanders dispose of an estimated 2.46 million tonnes of waste to landfills each year (Ministry for the Environment 2011). Plastic waste represents an estimated 8% by weight of landfill. This means approximately 200,000 tonnes of plastic ends up in our landfills each year of which roughly half is packaging*.
Between 2002–2004 and 2007–2008, the proportions of plastic waste, organics, glass, and sanitary waste have increased in the New Zealand waste stream, while rubble, paper and metal waste have decreased. These changes reflect changing consumption patterns, recovery rates of recyclable materials, and construction activity.
According to the Ministry for the Environment's Environmental Report Card by international comparisons, New Zealand has a low proportion of paper disposal, average proportions of glass, organic waste, metal and plastic waste disposal, and a high proportion of 'other' waste disposal compared with other members of the Organisation for Economic Co-operation and Development (OECD).
* Based on extrapolated plastic packaging waste to landfill from estimated total plastic waste
What is Waste Minimisation?
Waste minimisation as defined by the Waste Minimisation Act (2008) means:
- The reduction of waste, and
- The reuse, recycling, and recovery of waste and diverted material
This can be achieved through waste prevention and source reduction, and the design, purchase, manufacture or use of products and materials which reduce the amount of waste generated.
Waste prevention is not recycling, which is an effective way to manage waste materials once they have been generated. Waste minimisation actually reduces the amount of raw material used and therefore the amount of wasted resources discarded.
Avoiding the creation of waste is the most sustainable of waste management techniques. However, in New Zealand per capita waste creation continues to increase. As one example, general packaging consumption per capita has increased 14% over the past five years with plastic packaging consumption increasing at a slightly higher rate of 16.5%. (31kg plastic packaging consumed per capita in 2003 compared to 36 kg plastic consumed in 2008.) [Source? Is there anything more up to date?]
Insert mass balance graph? Sarah recommends getting it professionally redesigned if we do as difficult to read
Plastic Packaging
A number of OECD countries have set mandatory targets to slow consumption. In Germany and The Netherlands, for example, per capita waste generation has fallen as a result of policies introduced in the late 1980s. In New Zealand the preferred option has been to set voluntary targets through the 2002 New Zealand Waste Strategy although the Waste Minimisation Act now provides a legislative framework to introduce priority products with mandatory reporting requirements.
Many businesses are still unaware of the cost of waste disposal and many companies could make substantial reductions in their waste, and therefore, disposal costs. It has been demonstrated in Europe that companies could save around 1% of their turnover by implementing a systematic waste minimisation programme.
What are the benefits of effective waste management?
Effective waste management offers a range of benefits including:
- Cost savings that go directly to the bottom line (reduced raw material consumption, reduced waste disposal cost savings due to reduced volumes and recovered value of wastes)
- Competitive advantage
- Reduced impact on the environment
- Improved public perception
- Development of new and more sustainable processes
- Development of new products
How do I start a Waste Minimisation Programme in my company?
Prevention is better than cure. Recycling and treatment carry higher costs and can lead to pollution, while dumping or discharge usually carries the highest cost of all.
Follow the waste minimisation hierarchy for the best long-term benefits and look for solutions for your organisation which are as close as possible to the top of this hierarchy. The waste hierarchy identifies possible waste disposal options and ranks them in order of increasing environmental impact.
The aim is to work your way up the hierarchy from disposal until you end up eliminating all waste where possible.
- Eliminate - avoid generating/designing out waste
- Reduce - minimise the amount of waste you produce
- Re-use - use items as many times as possible
- Recycle - recycle what you can only after you have re-used it
- Dispose - dispose of waste in a responsible manner
Steps in Waste Minimisation
A systematic approach begins with commitment from the CEO or senior management and the appointment of a team with defined key performance indicators. The next step is to quantify and cost your wastes. The best options can then be ranked, costed and implemented. Reporting on successes provides feedback and maintains momentum. It also enables future targets to be set.
Step 1- Commitment All successful waste minimisation programmes begin with senior management commitment. This ensures that all individuals within your organisation work together in a positive manner to gain maximum benefit from the initiative. Start by identifying one or two areas which will bring about immediate savings for your company.
Step 2 - Assessment Most companies find it beneficial to appoint a team leader or "champion" to co-ordinate and facilitate their waste minimisation programmes. Involving teams and champions helps to increase staff awareness at all levels and motivates individuals to take action and participate.
Carry out a waste audit and collect data on quantities of waste generated and the disposal costs. Collecting baseline information is an extremely important phase of a systematic waste minimisation programme for two reasons. First, the baseline information should be a benchmark against which to measure future improvements and cost savings. Second, the information is crucial for identifying priority areas and setting achievable waste reduction targets.
Information should be collected in a systematic manner to ensure that as complete an initial assessment is made as possible. Begin a paper or electronic database of all information collected.
To start the assessment, use a process flowchart to map your company's inputs and outputs. Start by looking at your company or site as a whole and identify the main raw materials and utilities used - and the wastes produced. Determine the cost of each input and output, the quantities of materials used and the costs associated with different forms of wastage. This will identify the areas of business producing most waste, and which therefore require priority attention in a waste minimisation review. Use information which is readily available or make best estimates initially.
Remember waste is not just discarded materials. It includes the cost of wasted raw materials, rework, lost production time, waste treatment costs, wasted labour, loss of materials to atmosphere and to the drain, as well as the excessive use of energy and water.
A waste survey helps to identify areas that may have been missed from process mapping. This is a valuable tool to produce a mass balance of the materials used by the company or site. Waste survey teams are most effective if they include representatives from process or site services, production and management. Use graphs, charts and simple diagrams to present findings.
The quantities of all raw materials, energy and wastes should be provided for an annual period. Note that the units should be consistent, for example for different solid materials, for energy consumption and for water/effluent - this allows them to be compared in a meaningful way today and in future years.
Step 3 - Rank Options Identifying priority areas for waste reduction follows the data assessment phase. An assessment table can be used to summarise all the key data collected about your company's inputs and outputs. This will allow you to identify priority actions and rank options which will provide the best cost savings through improved efficiency and waste reduction. Use a ranking system to identify priority areas to tackle in terms of cost savings and also highlight obvious areas for waste reduction.
Step 4 - Prepare and Implement an Action Plan Finally prepare an action plan to implement your step-by-step approach to waste minimisation. Make sure that the action plan includes realistic and achievable waste and reduction targets which have been agreed by top management. Involve all staff when implementing the action plan and provide regular feedback to them. Provide feedback to all your staff – this will help to keep momentum going for the waste minimisation programme and encourage staff to look for future waste minimisation ideas and initiatives. Review progress against targets at least once a year.
Segregation of wastes
To maximise your ability to manage your waste, segregation of each waste type is vital.
Here are some simple tips to segregate your waste:
- Try to segregate waste and material for re-use at source — this is much easier than sorting afterwards
- Use colour-coded bins for different waste types
- Sort waste according to type, grade and colour
- Set up specific collection points for different types of materials at convenient locations (canteens, offices, shop floor, production area)
Hazardous waste
Certain wastes are classified as hazardous - a very broad term for a wide range of substances that present different levels of risk. Some present a serious and immediate threat to the population and the environment, eg those which are toxic could cause cancer or infectious disease. Others, such as fluorescent tubes or cathode ray tubes in televisions, pose little immediate threat but may cause long term damage over a period of time.
Any business handling high-risk wastes should already be working with their waste contractor to dispose of them safely. The action you need to take will depend on the types of waste your business generates.
You will need to:
- Think about the range of wastes your business generates. Hazardous wastes will need to be collected and disposed of separately.
- Think about how to reduce the amount of waste your business creates – producing less will make life easier and could save you money - organisations with efficient resources, which adopt sustainable practices, reduce waste and pollution.
To assess whether your waste is potentially hazardous you can consult the New Zealand Waste List on the Ministry for the Environment website and search for keywords such as 'plastics' and 'inks'. The site provides guidance on the management of hazardous wastes including disposal.
Waste Minimisation Funding
Good funding sources exist to help companies and organisations develop projects that reduce waste going to landfill.
The Ministry for the Environment has the Waste Minimisation Fund (WMF) which is a contestable fund worth around $12 million a year. There are usually two funding rounds each year. Several Plastics NZ member companies have successfully applied for project funding under the WMF.
Funding is available for feasibility studies ($10,000 minimum) and projects ($50,000 minimum). Funding can be used for operating and capital expenditure required when undertaking a waste minimisation project.
The WMF will pay for cost relating to the following:
- Personnel
- Administration
- Consultants and contractors
- Purchase of capital assets and other capital costs
- Venue and equipment
- Promotion and dissemination of information
- Financial, legal and information technology (IT) expenses
- Travel and accommodation
- Other miscellaneous costs
The WMF will not fully fund a project so other sources of finance needs to be available. The amount of contribution is not specified but the Ministry for the Environment suggests that this should be at least 20% of total costs.
Further information, including a Guide for Applicants, can be found on the Ministry for the Environment website.
Some local councils also provide funding for waste minimisation projects in their area.
Plastics NZ will support, and in some cases work with member companies on WMF funding applications and projects. Contact us for more information.
Case Studies for Waste Minimisation in the Plastics Industry