EPS News
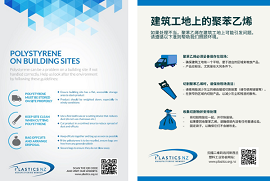
Recycling Polystyrene from Building Sites
Mandarin Version
The use of expanded polystyrene in building has been around for many years due to its qualities as a strong, durable and lightweight material with excellent thermal properties – and it is also great for recycling.
The Plastics NZ Expanded Polystyrene Sector Group is keen to help builders tackle on-site issue. Members realise that there is an underlying need to inform and educate site managers and staff
The EPS Sector Group have updated their Building Site Information and produced a Mandarin version to assist those working with polystyrene on construction sites.
- Download the Mandarin Version
- Download the English Version
(March 2021)
EPS Industry announces the launch of Airpop
New Zealand’s EPS (Expanded Polystyrene) Sector Group, in association with Plastics NZ, is proud to announce the launch of Airpop – a new name for a product that has been relied on by many since the 1950s.
Already well known as a designation for EPS products across Europe, the Airpop New Zealand brand brings together leading local manufacturers in an effort to improve education about and recycling rates for expanded polystyrene.
“Many people don’t realise that Airpop products, made of expanded polystyrene, are actually 98% air. Only 2% of the product is made of plastic – and that 2% can be recycled many times over,” says Rachel Barker, CEO of Plastics NZ.
In New Zealand, Airpop is commonly used in electronics packaging, protection systems like helmets and children’s car seats, for keeping fresh produce chilled and as insulation and ground fill in construction projects.
“When produced by accredited manufacturers and handled responsibly, many Airpop products can last for decades. Those that are created for a single-use purpose, or product which is leftover, can be recycled into a myriad of other products,” says Barker.
“We feel that it’s important for us to teach New Zealanders about how to better use and recycle Airpop, to ensure it has a positive impact on our lives – and our environment,” she says.
Kiwi consumers and businesses wanting to know more about Airpop manufacturing and recycling are encouraged to visit the Airpop website.
(December 2019)
Recycling Polystyrene from Building Sites
The use of expanded polystyrene in building has been around for many years due to its qualities as a strong, durable and lightweight material with excellent thermal properties – and it is also great for recycling.
Unlike many other building products, expanded polystyrene can be recycled countless times without losing quality. As a result, we are now seeing a prevalence of recycled content in the polystyrene products we use, which means a more positive environmental impact due to less wastage.
Advances in technology in manufacturing have helped increase the possible uses for expanded polystyrene and its potential for recycling. Building products now account for nearly three quarters of the 8500 or so tonnes of expanded polystyrene manufactured in New Zealand annually, which is primarily made up of thermal insulation, and a substitute for concrete called “waffle pods”. In the case of pods, the recycled content can be as much as 50%.
Throughout New Zealand, customers can benefit from a recycling service offered by expanded polystyrene manufacturers who are members of Plastics New Zealand. Customers receive bags to collect their clean offcuts at their building sites, and a collection service. The “waste” is then reprocessed and reused in other products, rather than going to landfill. In providing this service, manufacturers demonstrate their commitment to the industry’s waste minimisation initiative, and customers avoid the need to manage and store a material that, if not handled appropriately, can end up causing problems such as litter.
The recycling initiative is available in all major New Zealand cities, however tradespeople who are using polystyrene products need to be proactive when dealing with their waste in order to benefit. The point is: why pay landfill fees when manufacturers offer a service that benefits customers and the environment.
Plastics NZ Business Manager Ken Sowman says: “All parties have an important role to ensure these schemes are a success – reducing litter on building sites and reducing waste going to landfill.
“However,” Ken adds, “builders can also take advantage of having their material cut to specific size to avoid creating waste offcuts in the first place.”
For more information please discuss with our EPS Manufacturing Member Companies involved in this inititative:
Barnes Plastics Ltd
Expol Ltd (Including Long Plastics Ltd)
EPS Foam Ltd
Hope Moulded Polystrene
Koolfoam Ltd
Styrobeck Ltd
PLEASE NOTE:
The Building Site EPS Collection Services is for offcuts/waste of NEW EPS products eg Waffle Pods, underfloor insulation etc, that have been supplied by a particular company direct to their customers site.
This service is NOT available for the packaging coming from other goods and services bought onto the building site ie packaging of electric goods, appliances, bathroom cabinets etc. This service is NOT for Demolition Waste.
For EPS Packaging Recycling on Building Sites or for Demolition Waste, you would need to contract a bin service from the likes of Waste Management or other Local Recycling Company offering this service
To download the Polystyrene on Building Sites Sheet as a pdf click here
Testimonials
Mike and Matt both manage concrete floor laying companies. Both their companies are using and benefitting from the recycling service their waffle pod manufacturers offer, and helping to maintain litter-free building sites.
“Handling polystyrene on building sites to avoid problems is ‘just good management’” says Matt. “We don’t get the product until we’re ready to use it, and we very rarely have problems.
“For clients, dealing with waste that’s light and bulky is difficult. The service we get makes removal easy, and the use of what’s not used is great. It’s also a great saving for us.”
For Mike, the ease and the savings make getting a service a big plus. “I’m a very happy customer,” he says. “We order about 5000 pods a month, and we get a collection almost every day for the product we don’t use. This saves us about $400 a week that we’d have to pay if the waste went to landfill.”
(June 2015)